Table of Content
The city is exploring a variety of potential ways to address looming budget deficits — including more parking meters and new taxes on rental car companies and parking garages. You need plenty of space on your property for a crane and semi-trucks to deliver and install your home module sections. Certain design limitations exist since contractors must move the modules onto a truck for delivery. You often need to own or buy a piece of land before installing the modular home.
Also, many houses built on a slab foundation have their plumbing under the slab, which has to be rerouted and pushes the price up. When building an extension, you’ll find that you might have to dig the foundation deeper than the existing foundation to match updated building codes. If your house is old, you might have to underpin the existing foundation to avoid possible structural damage from attaching the extension to it. There are risks in raising a house and repairs that should be factored into the total cost. There are three main types of basements to choose from based on your specific location, soil, and groundwater conditions.
Commodore Homes
The house is placed on a steel chassis and transported to the building site. Deep Foundation – A deep foundation is typically used in poor soil conditions, unlevel ground, or if the structure needs to be raised to prevent flooding. Deep foundations are constructed from steel, wood, or reinforced concrete, and require the assistance of a structural engineer. If grading is required to direct water away from the house, fine grading and leveling land costs $0.40 to $2.00 per square foot.

I find that if there is some friction in the hose, it allows the riving knife to deflect, which can cause any problems. Instead of grappling with huge pieces of wood and searching for how to carve them correctly, you can do it in a blink of an eye if you have this DEWALT DW745 Table Saw. At first, we were dubious about such a rip ability, but after 100’s of 4’x8 “plywood sheets, the rip guide helped for rough work. It doesn’t have a lot of blade teeth, and this machine is better suited to wild cutting activities rather than polished finish cuts. The veiled blade renders dust accumulation a sight, and you can hardly see any dust at all if you get the right dust extraction vacuum. Finally, the rip fence is smooth and accurate more than anything I’ve ever seen.
Cost of Buying From One of the Best Modular Home Manufacturers
Clayton Modular Homes prices range from $70 to $200 per square foot or between $30,000 and $200,000 depending on the size, model, and delivery distance. Clayton operates nationwide and offers more than 175 floor plans ranging from 1,000 to 2,280 square feet. Champion Modular Homes prices range from $90 to $140 per square foot and are typically built and delivered within 2 months. Champion offers over 2,000 pre-designed home plans ranging from 400 to 2,400 square feet that are available nationwide.
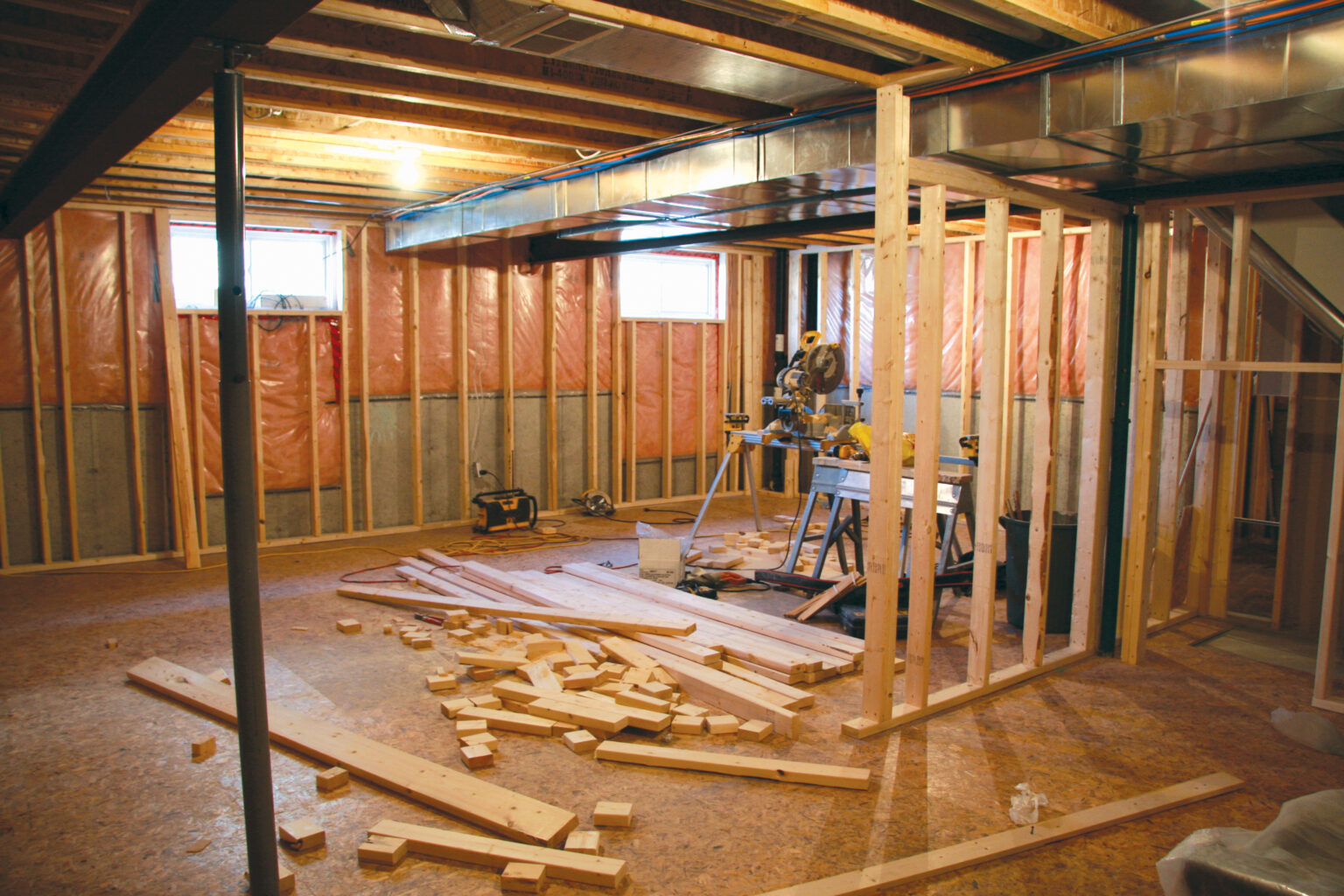
Both single wide and double wide manufactured homes are placed on this type of foundation. Off-frame – The most-common, highest-quality modular homes are lifted off of their transport frame and placed onto a permanent foundation, which makes them more expensive and difficult to relocate. These homes can appreciate in value like site-built homes since they have lasting foundations, and the buyers also own the land.
Planning and Permit Prices
Modularity involves constructing sections away from the building site, then delivering them to the intended site. The modules can be placed side-by-side, end-to-end, or stacked, allowing for a variety of configurations and styles. After placement, the modules are joined together using inter-module connections, also known as inter-connections. The inter-connections tie the individual modules together to form the overall building structure. Footings add $5,224 to $15,672 to the cost of the foundation, with prices growing as the footings go deeper and wider.
Discussions on hosting and services offered by managed service providers. This includes reviews and general questions and answers about the managed services segment of hosting. Whether you purchased managed hosting or hired someone to manage your server, you're in the right place. Word HTML is the perfect tool to edit the source code of WordPress articles or any other content management system when their built in composer doesn't provide all functionalities we need. Compose the content right in your browser window without installing any extension or plugin to handle the syntax highlighting and other text editing features. Modular construction is one way to keep your initial overhead investment in a home reasonable.
Looking for Modular Home Builders near you?
Fortunately, Newfound and Labrador boasts several reputed modular home builders. The good news is that modular homes are an exceptional alternative to conventional homes, and are becoming popular among homeowners in Quebec. Quebec is an excellent choice if you’re also looking for a peaceful and beautiful place to build a new home. However, remember that building a custom home requires plenty of time, money, and planning. The two small modular home models, both under 2,000 square feet, feature two bathrooms and three bedrooms each. Courtesy of Southland HomesThe quality of artistry is another pillar of Southland, which you’ll see as you browse the collection of modular properties.
Not only do I love the versatility it offers, but also the custom size options are great for any room. It is the perfect sofa for napping, watching a movie, or reading a book,” says Amanda Sacy, design manager at Juniper Holiday + Home. "Nine seat section options offer endless configuration opportunities so you can create a sofa that spans a great room, or something that better suits a small space,"Floyd Co-Founder and CEO told Living Cozy.
The best modular home manufacturers offer competitive wages and amiable working conditions, retaining staff for longer and promoting potentially better craftsmanship. With all of that background on choosing the best modular home manufacturer, it’s time to get down to business. For shoppers who’d rather not perform an internet search for “local modular home manufacturers,” here is a list of modular home manufacturers that are trusted options. The home site’s proximity to the facility, the number of sections, and freighting availability all play a part. Folks that live outside of the factory’s designated shipping area may have to pay additional fees to have their homes delivered as well. You have many choices when it comes to building the right modular home for you, but you will be given a set number of options to choose from.
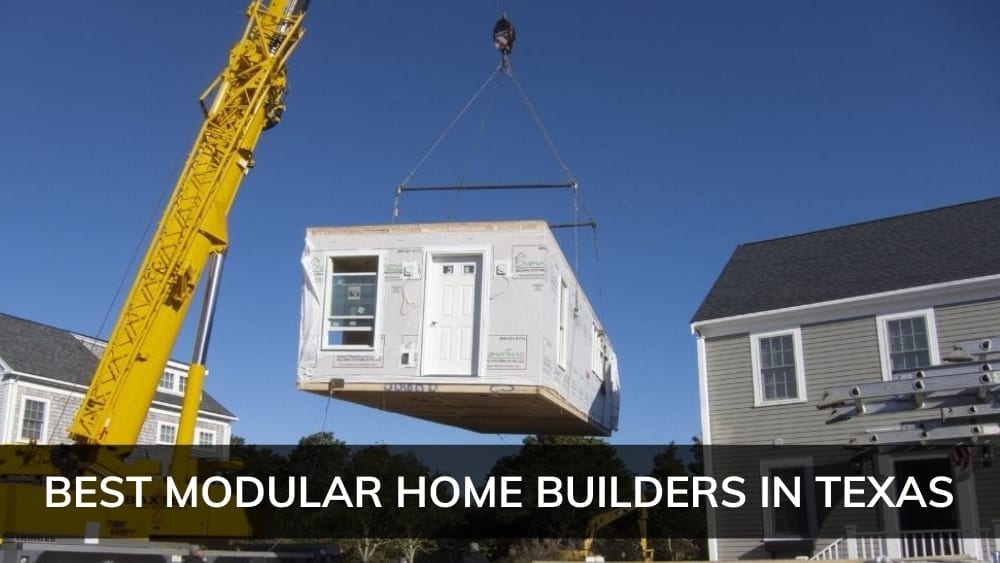
The average cost to build a stick-built house is $100 to $200 per square foot. Modular home prices range from $80 to $160 per square foot on average. Banks tend to offer fewer financing options compared to site-built homes.
If extra footings are required, add $6.53 per square foot to the cost. Other types of modular buildings that are offered from a company like Allied Modular include a guardhouse, machine enclosure, press box, conference room, two-story building, clean room and many more applications. Modular design inherently combines the mass production advantages of standardization with those of customization.
No comments:
Post a Comment